Stable, Like a CAMEL
Important Notice:
Our company name is "Shenzhen Camel Die".
Please note that "Camel Die" is a separate entity and is not affiliated with us in any way. Our email address is @cameldie.com
We urge our customers and partners to verify the correct contact information to avoid any confusion or miscommunication.
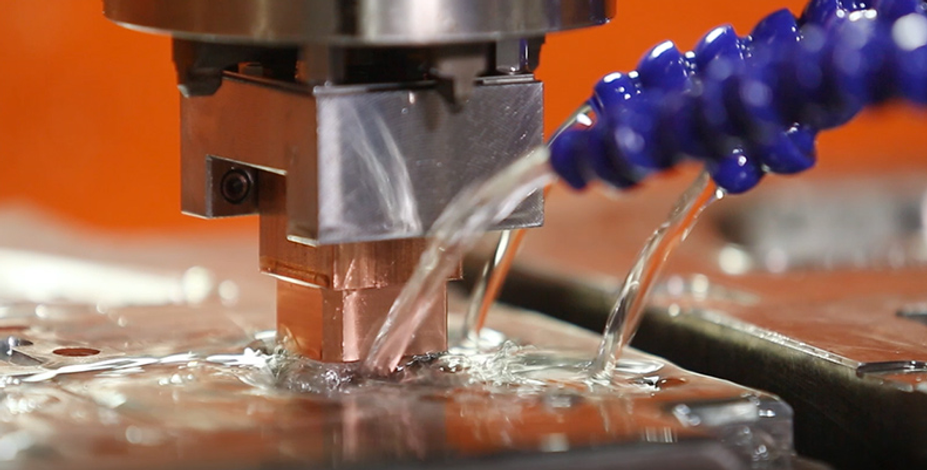
FLOW PATH
How long does it take to turn ideas into reality and drawings into real products? Generally, different industries have different production cycles. For the die casting mold industry, the processing volume is determined according to the size and structure complexity of the parts.
CAMEL DIE got a set of a die-casting mold project from one of our American customers in May of 2020. This die-casting part is a metal gasket used on aircraft seats. Due to the product design updates and change in the number of cavities from 2 cavities to 4 cavities we provided the updated quotation within 24 hours with all related details such as the mold base, tool action (slider requirement), cavities, estimated casting machine size for the first trial, estimated die casting mold size(mm), estimated mold life, design confirmation timing, steel cutting to T1 (weeks), mold cost and freight cost. etc. CAMEL is committed to improving our response speed. Serving our customers and fulfilling their requirements is our standard.

When our client wanted to proceed to start this project however, they needed to expedite the lead time to 5 weeks instead of the 8 weeks we had originally quoted. Had this requirement not been met, we would have stood to lose the order. After strong communication with our team of experts and the detailed evaluation of this project, we determined that it could be completed in advance within the required time. To support long-term cooperation with our customer, we proceeded with the designing in advance before we got the order. This saved us one week of lead time, and we were thus able to adjust the processing schedule accordingly. With our strong motivation to go above and beyond our customer’s expectations to build quality molds we thrive on being flexible with lead time without cutting any corners.



After we confirmed the completion of the required changes with our customer the order was promptly confirmed. Upon receiving the order confirmation, we immediately began to prepare for the die casting mold design and submitted the product analysis report in one working day. In the DFM report, all details were confirmed with our client, such as the parting line, injection pin, visible areas, inserts, split lines, ejection location, engraving & cavity, radii, machining & allowance, complete information of the die-casting machine, clamping slot, etc., as well as some suggestions about the parts.
The mold flow analysis report was provided within 3 working days and the 3D mold drawing in 2 working days. Our teamwork cooperation and communication were smooth and efficient and because of that the design confirmation was completed in one week.
During the mold building process, we strictly followed our project management system in order to ensure quality control. If there were any pending questions that required confirmation with our clients our team ensured that a prompt reply was provided with our suggestive solutions so that everything remained on schedule. Because of our teams’ strong work ethic and attention to detail the entire project went very smoothly and in fact we were able to finish the project one week in advance which our client was incredibly pleased with.
During the mold building process, we made sure to keep our client up to date on every step and detail to ensure we were all on the same page. An example of this is that we submitted the tooling schedule and weekly report status with pictures of the mold process.

After we finished the mold build and completed the T1 trial, we provided our client with the trial report with detailed photos of the mold and parts. We also provided the die casting machine parameter data.
The FAI report was provided in 3 working days to ensure all measurements were in the correct tolerance.

After inspection by our engineers, we confirmed that there were no issues with the samples and sent 5-10pcs to our customer for assembly inspection. The whole project went exceptionally smooth.
As normal it took 7 days by express freight for our client to receive the samples. After inspection and measurement confirmation our client provided feedback to CAMEL If there were any updated suggestions.
With detailed review and confirmation our client approved these samples after 2 weeks then informed us to arrange the mold shipment. We promptly proceeded with inspecting all mold components, assembling the mold, and running one more trial before shipment.

CAMEL has more than 12 years of experience in the mold industry, and in order to support our customers well, we have also developed multiple after-sale partnerships in the customer's area, which can provide mold landing services and follow-up parts replacement services, as well as technical support if needed.
Our aim is to make a good mold - stable like a CAMEL!
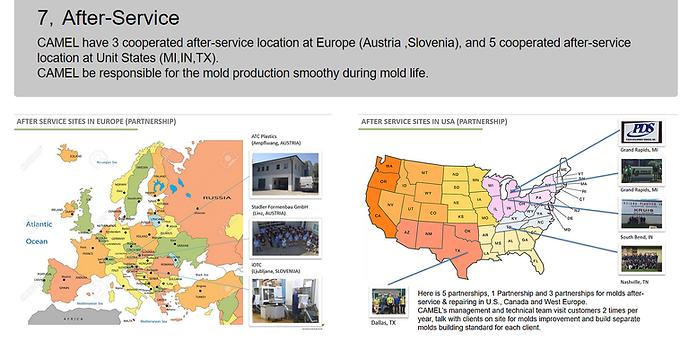