Stable, Like a CAMEL
Important Notice:
Our company name is "Shenzhen Camel Die".
Please note that "Camel Die" is a separate entity and is not affiliated with us in any way. Our email address is @cameldie.com
We urge our customers and partners to verify the correct contact information to avoid any confusion or miscommunication.
We aim to create a long-term partnership
that will be based on competence, reliability, and engagement with customers.
標題 1
標題 1
12-Step Design Process,Pre-Production Process Design and Verification,Extensive Industry Experience,make sure to deliver high-quality die-casting molds for seamless mass production
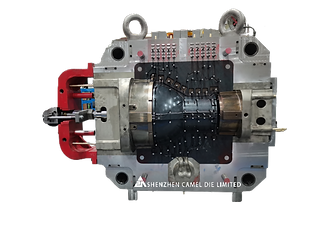(1).png)
(1).png)
Fixed Side
Movable Side
(1).png)
(1).png)
(1).png)
(1).png)
12-Step Design Process: Ensuring a high first-trial success rate for your die-casting molds.
We have developed a 12-step standardized design process for die-casting molds, ensuring a high success rate for the first mold trial. This process begins with understanding customer and part requirements and concludes with comprehensive simulation verification. Our systematic approach guarantees precision and reliability at every stage.
Key Features of Our Design Process:
-
Customized Design Parameters: We utilize a proprietary application to calculate die-casting mold design parameters. This tool, based on NADCA standards and our extensive experience, ensures uniformity and accuracy in every design.
-
Comprehensive Simulation: From flow pattern analysis to final simulation, we leave no stone unturned to ensure optimal mold performance.
Our 12-Step Design Process:
1. Understand the quality requirements of castings
2. Determine CNC fixture
3. Determine casting processing parameters
4. Calculate total gate cross-sectional area
5. PQ² Calculation
6. Determine flow pattern
7. Design gates and runners
8. Simulation analysis
9. Venting and overflows design
10. Cooling system design
11. Die structural design
12. Final simulation analysis
Pre-Production Process Design & Verification: Guaranteeing a seamless transition to mass production.
To ensure a smooth transition to mass production, we have established a dedicated Trial Production Department. This department is equipped with state-of-the-art machinery and inspection tools, enabling us to verify mold performance and production processes before delivery.
Key Advantages of Our Pre-Production Services:
-
In-House Trial Production: Equipped with 4 die-casting machines, 13 CNC post-processing machines, and advanced inspection equipment (including CMM, X-Ray, 3D scanning, and material analysis), we can conduct trial production to validate mold performance and process efficiency.
-
Faster Time-to-Market: By identifying and resolving potential issues during the pre-production phase, we help customers achieve mass production in the shortest possible time.
-
Urgent Production Support: For customers needing immediate product samples for end-user testing, we can produce urgently required parts, saving valuable time during mold transportation.
(1).jpg)
(1).jpg)
Extensive Industry Experience: Delivering proven expertise to ensure your project’s success.
With a proven track record of designing and manufacturing over 1,000 sets of molds across various industries, we bring unparalleled expertise to every project. Our experience spans a wide range of applications, including:
-
Automotive Components: Precision molds for critical automotive parts.
-
Communication Equipment: High-quality molds for telecom and networking devices.
-
Outdoor Lighting: Durable molds for streetlights and outdoor fixtures.
-
Office Furniture: Innovative molds for ergonomic and stylish furniture.
-
Industrial Machinery and Appliances: Reliable molds for heavy-duty and consumer appliances.
(1).jpg)
(1).jpg)
Why Choose Shenzhen CAMEL DIE?
-
Proven Expertise: Our 12-step design process and advanced simulation tools ensure precision and reliability.
-
Seamless Transition to Mass Production: Our pre-production capabilities minimize risks and accelerate time-to-market.
-
Customer-Centric Approach: We prioritize your needs, offering tailored solutions and urgent production support when required.
-
Extensive Industry Experience: With over 1,000 molds delivered across various sectors, we bring unmatched knowledge and expertise to your project.
“Stable, Like a CAMEL” – Trust Shenzhen CAMEL DIE for your die-casting mold needs, where stability, precision, and efficiency are our promise.
Our success is based on highly qualified and trained employees. Systematic development of skills helped us in building a strong, experienced, and innovative team. Continuous improvement of our knowledge ensures sustainable success.
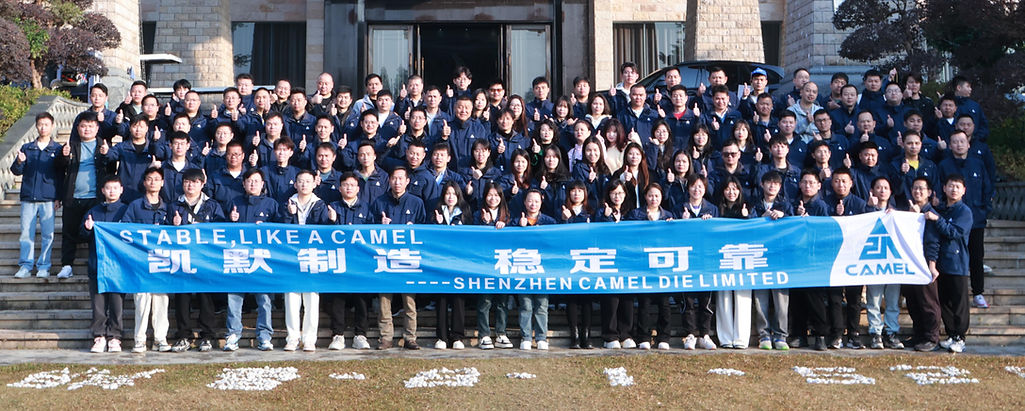