Stable, Like a CAMEL
Important Notice:
Our company name is "Shenzhen Camel Die".
Please note that "Camel Die" is a separate entity and is not affiliated with us in any way. Our email address is @cameldie.com
We urge our customers and partners to verify the correct contact information to avoid any confusion or miscommunication.
What is Die Casting
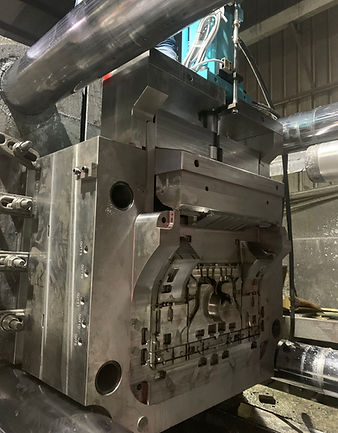_j.jpg)
Die Casting Definition
Die casting meaning a metal processing process in which molten metal is injected into the machine, allowing it to cool and harden then formed into a specific model. Die casting molds are cycled under standard conditions to produce a dimensionally or functionally alloy product.
Die castings are used in a wide range of applications, lighting, automotive, aviation, large equipment, furniture, engines, motorbikes, special properties, and mass production have led to die casting is used in life.
Cast metal
The most used metal materials are zinc, aluminum, magnesium, copper, lead, tin.
Specific die casting metal includes:
Aluminium: ADC12, A380, Alsi9Cu3, Alsi12Cu1, AC4CHT6, YL102, YL112, YL113.
Magnesium: AZ91D, AZ80, AZ31B, AZ40M, AZ31, ZK60, ZK61, AM60M, ME20M, ZK60A, ZK50B, ZK51A.
Zinc: Zamak2, Zamak3, Zamak5, Zamak7, Zamak8.
Copper: Brass, Bronze.
Market Distribution Of Die Castings
China is the largest producer of die casting molds, North America is the largest use region, India is the first producer, and Italy is the first echelon in the European region. So when you are a part of die casting, the below image will help you understand how the global die casting market is distributed. We provide a constantly updated list of global die casting manufacturers here for you.
Advantages Of Die Casting
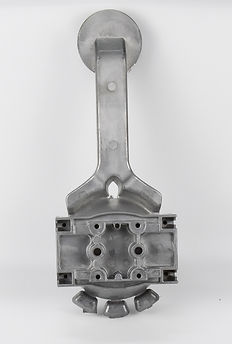.jpg)
-
Higher impact strength than plastic, especially large machinery and equipment such as trucks and cars
-
More stability in dimension is a very important element. For example, POM or other plastic products with special shapes are transported from Asia to Europe, the size will change under the influence of temperature, but die castings will never have such a big change.
-
Product has a longer life,special parts like robot arms, engine covers, LED, etc., after the long-term operation and high and low temperatures, there will still be no changes in material and strength
-
More resistant to corrosion,some ship components, chemical vessels, weapon components, etc. need to be immersed in liquid or exposed to the gas for a long time without oxidation and decomposition
-
Wall thickness also does not affect, some parts like large furnaces, clocks, aerospace components, and trucks are often so thick and strong only casting can achieve the required strength.
Disadvantages Of Die Casting
-
More dangerous when casting in workshop,more requirements in terms of safety in production,more insurance and protection
-
All other types of casting except die casting are not suitable for thin walls
-
Heavier than plastic products, more shipping costs, and packaging costs
-
More demanding on the environment,dirtier and messier workshops, exhaust and effluent discharge not easily dealt with
-
No complex die structures can be used, for the same product, plastic molds can complete more structures, die-casting molds need secondary processing, CNC, WEDM
-
More cost than plastic, like materials, tools, transport, environment, and secondary processing
.jpg)
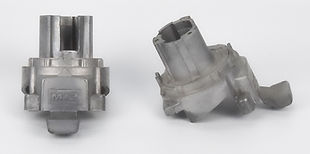.jpg)
Types of Casting
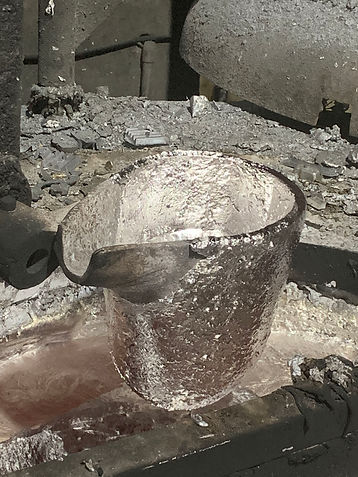_.jpg)

-
Die casting, a high precision casting process is usually used for die castings with dimensional requirements, such as aerospace, automotive, custom equipment, etc., precision components, all processes are completed in the machine, including injection, pressure-holding, and cooling.
-
Sand casting, a low-cost casting method, half manual, and half machine operation, multiple layouts in one cavity, molds and cores no need high cost, no high requirements for mold appearance and steel hardness, subsequent appearance treatment after forming, almost no requirements for product density and accuracy.Can be used for a wide range of casting materials.
-
Investment casting, a complex process of casting for die castings with complex shapes and structures. The first step is to make a wax mold with a similar structure as the plastic mold, fill it with wax and shape it (the shape of the wax is the shape of the final die casting); the second step is to take the product out and coating it evenly with two special materials, the first coating is fine to make the surface of the die casting smooth and ensure that the wax product will not crack easily at a certain temperature after air-drying the second coating is applied, the second coating will form the mold of the part shell, the melting point of the coating is a little higher than the melting point of the die casting; the third step into the furnace, the surface material after high temperature to form the shell, the wax has been melted, Investment Casting is formed, pour the melted die-casting material and cover for insulation, crack the shell to remove the part.
-
Low-pressure casting, a simple casting method that differs from high pressure die casting in three ways: 1. the molten metal is injected into the die using air, 2. the furnace is placed at the bottom of the die to facilitate air pressure, and 3. the shape of the product must appear to be a mirror image to facilitate pressure balancing within the die. low-pressure casting is not suitable for most die castings. The reason sees here.
-
Gravity die casting, the simplest form of casting, with only a cavity and a core, not even a machine to clamp it, the molten metal is poured in through the top of the die and knocked out when it cools, suitable for small batches of die castings.
-
Vacuum die casting, a method of improving the quality of casting, usually for magnesium alloys, where the air is pumped out of the cavity before the molten metal is fed in (some special dies are injected with oxygen after the air has been pumped out) and then the metal is injected, resulting in a die casting with fewer pores and high density, which is more complex in batch production conditions and prone to explosions caused by leaks.
What's The Difference Between Die Casting, Sand Casting, Gravity Die Casting, Vacuum Die Casting, Investment Casting?
-
Vacuum die casting is the best in quality
-
Die casting is the highest in efficiency and good in the casting of thin rib
-
Gravity die casting is the best in cost
-
Sand casting is best in small batches
-
Investment casting is best on complex structures
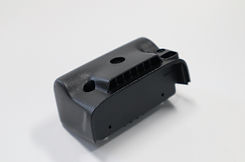

What Are The Factors Affecting Casting Quality?
-
Stable machine, stable material supply, no pores, and residue.
-
The core and cavity are at the specified temperature during the heat treatment process to ensure that the material is in the best performance. It is important to choose the right die casting steel for the cavity and core because the production is always in a high-temperature environment.
-
The metal material has no impurities and the temperature is suitable, then the surface of the die casting will be smoother
-
The gate, slag strap, and ejector design in the mold are reasonable, and the casting process is smooth, without excessive pressure and material waste
Points Of Die Casting Mold Design
-
In the design process, the following points in the 3d part drawing should be avoided:
-
Sharp corners.
-
Little or no draft.
-
Heavy walls.
-
The following points of mold design should be noted(Make Moldflow analysis report will be better):
-
Gate.
-
Runner.
-
Exhaust seat.
-
Cooling.
-
The following points need to be designed before testing:
-
Support pillar as much as possible
-
Pre-heating temperature according to material requirements
-
Control cycle time
-
Control mold temperature and metal temperature
-
Machine size

Difference Between Die Casting And Plastic In The Environment


According to scientists, fish, birds, and animals were killed by plastic floating in the ocean due to accidental eating. Die-casting parts are rarely discarded in the ocean. Even if they are discarded in the ocean, they will sink to the bottom of the sea. Will be recycled again, the discarding of die castings will have very little environmental harm in the future, but the discarding of plastic will have a very bad impact on the environment.
Why Does The Color Of Die Castings Change?
When the die casting material is melted, some iron filings will be mixed and introduced into the furnace. After the casting is completed, the iron will be oxidized with oxygen in the air. the surface color of the die casting will become different. If your requirements are stricter, vacuum die casting will be better.
Processes After Die Casting Production
-
Rough and precision punching.
-
Deburring, clean the hole.
-
CNC, EDM, WEDM.
-
Surface corrosion protection.
-
Sandblasting, oil blasting, electroplating, and even positive oxidation.