Optimization of Process Structure for Castings
- Delia Wu/CAMEL
- Jan 22, 2021
- 8 min read
Updated: Aug 13, 2021
Optimization of Process Structure for Castings
Abstract: In the design of die casting mould, more consideration is given to the curability of the mould itself, such as runner, overflow, temperature, ejection, etc. However, if the technological requirements of subsequent casting machining are not well considered in the design stage of the mould, the machining difficulty of the casting will increase.
The production efficiency is reduced, which ultimately affects the machining production cost. Therefore, in the die design stage, not only the die casting process should be considered, but also the needs of subsequent machining should be considered more, so as to effectively optimize the die design scheme and improve the overall economic benefits of die castings. Die-casting has a series of characteristics such as high production efficiency, low cost, excellent appearance quality and long die life.
In production, The rationality of mold design determines the quality of castings and the production efficiency. Therefore, the whole mold design process needs to be fully considered in combination with casting characteristics, die casting equipment capacity, material characteristics used, customer special requirements and other relevant factors. However, in actual production, most die-casting mould designer take that demand of blank die-casting as the key point of design concern. However, the special needs of subsequent machining are ignored, and problems such as difficult positioning, uneven blank allowance and shortened tool life often occur in the machining of die-casting blank, which seriously affect the production efficiency of machining and the stability of casting quality, and eventually lead to the decline of economic benefits of enterprises. The following is a brief discussion on the influence of the structural characteristics of die casting molds on machining and how to optimize them.
1st Influence of Gate Design on Die Casting
The location of the ingate is one of the important links in the die design. The ingate design of the die casting mould is almost always based on the filling and forming of the casting.
Quality and flow state are carried out without too much consideration of the influence of blank on subsequent machining.
1, Influence of ingate Position on Cutting Tools
In many ways, the setting of the ingate location of die casting is the key and difficult point in the gating system design. Any negligence will cause unpredictable mistakes, which cannot be made up by the adjustment of die casting process. From the perspective of die casting production, the following basic principles should be followed in selecting gate position.
(1)Avoid closing the venting passage immediately after liquid metal enters the mold cavity, which is beneficial to removing the air in the mold cavity.
(2)As far as possible, branch ingates should be used less, so as not to interfere with each other and form eddy current and entrained air.
(3)The ingates should not face the core and cavity wall directly to avoid direct impact of molten metal.
(4)The ingates shall be placed at the thicker part of the casting to facilitate pressure transmission.
(5)The molten metal flow is the shortest to reduce energy loss and avoid too much cooling.
(6)The ingates shall not cause deformation during shrinkage of the casting.
(7)Set the inner gate as close to the important parts of the work piece. If the setting of ingate location can meet the above conditions without considering the subsequent machining of the blank, then the setting of ingate location can be said to be perfect.However, most die castings need to be machined in production. If the actual demand of machining for casting blank is ignored, it will definitely bring some unnecessary troubles. The main manifestations are: the influence of the residue after gate removal on machining positioning and intermittent cutting during machining of gate parts.
As we all know, intermittent cutting is a technological difficulty in mechanical machining, which can generate periodic vibration, make stripes or corrugated marks appear on the machined surface, resulting in an increase in the surface roughness value. Intermittent cutting in the cutting process makes the tool periodically stressed, which is easy to cause tool collapse and reduces the service life of the tool. In intermittent cutting, the operator has to adopt lower cutting speed spread and smaller feed, which affects the production efficiency of the machine and the worker.
Relatively speaking, the influence on positioning is smaller. When designing machining fixtures, more understanding and communication should be done to confirm the gate form and position of the blank, estimate the approximate size of the gate residue in the future, and try to avoid using the gate position as the positioning benchmark for machining.
Therefore, on the premise of meeting the die casting production, the ingate location setting also needs to take into account the technological requirements of subsequent machining, and reasonably arrange the ingate location of blank according to the actual technological process of machining. If you can't have both, it is recommended that the ingate be placed on an exposed and flat plane to facilitate polishing and reduce the allowance. Or the ingate location and size are placed evenly and continuously on the processing plane to reduce intermittent cutting.
1.As shown in picture 1, it is a common ingate location selection problem. Picture 1a that ingate is set on the movable die, and the ingate will remain on the circular plane in the future. From the perspective of die-casting technology, the ingate set on the movable die side is beneficial to the filling of molten metal and the die-casting production of castings. However, the ingate residue on the circular plane can be removed by subsequent machining, and the casting has beautiful appearance and no gate residue trace, but it will bring the problem of intermittent cutting. Fig. 1b is set at the fixed mold side, and the ingate will remain on the circumference of the casting in the future. In terms of die casting process, the metal liquid set at such ingate will directly impact the cavity wall of the mold, which is easy to adhere to the mold at the corresponding parts of the gate. After the ingate is removed in the future, ingate marks will remain on the circumference of the casting, affecting the appearance quality of the casting. However, the problem of intermittent cutting is avoided without machining the circumferential part.
2.The choice in actual production needs to be combined with the characteristics of their respective enterprises and comprehensively balanced with customer demand as the orientation. What should be emphasized here is that the design of die casting dies should take into account the needs of machining as much as possible.
2.Influence of Ingate Position on Machining Positioning Machining
1.Generally, a coarse reference on the blank should be selected for positioning, and then fine reference processing should be carried out. These coarse benchmarks require smoothness, reliability and consistency. There are mainly two selection methods for coarse benchmarks.
(a)When the dimension chain on the machined casting pattern does not take a certain non-machined surface as the design benchmark, the determination of the coarse benchmark will often select the largest plane, outer circle or inner hole on the blank, because these features can obtain the maximum positioning limit and ensure the accuracy and consistency of positioning.
(b)When the dimension chain on the machined casting drawing takes a non-machined surface as the design datum, the coarse datum must be selected, because the fine datum machined from this datum can represent the drawing in subsequent machining. The original design datum on is used as the process datum.If the gate appears in these areas, the casting positioning will be seriously affected. According to the machining positioning method, the corresponding optimization scheme is as follows:
(1)As far as possible, the gate position should not be selected on a larger plane for positioning or on a very accurate design.
(2)If the ingate must be placed on a larger plane for locating or on a design basis, consider multiple strands of feed and reserve the required position for positioning, as shown in Fig. 2. The middle area of the strand division is still a flat area, which can form a three-point-plane positioning (the same as the outer circle positioning) with other areas.
(3) When the casting allows, add process positioning bosses (see Fig. 3) to optimize machining positioning coarse datum level.
(a)The gate at the core side (b)The gate at the cavity side

Picture 1 Different Design of Gate Position
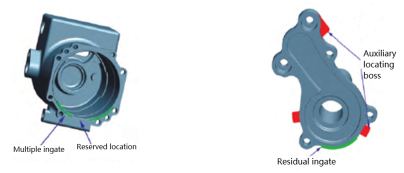
Through the above optimization scheme, the reliability of casting machining positioning can be improved. In addition, paying attention to the deformation at the gate and optimizing the gate removal process during die casting production can improve the machining positioning.
2nd Influence of Reserved holes
1.Influence of Reserved Holes on Position Tolerance
It is generally believed that the hole should be reserved as far as possible for the hole shapes that can be formed in the mold, so as to reduce the machining allowance, protect the hardened layer of the casting and ensure the good air tightness of the casting. However, the reservation of bottom holes sometimes raises another question as to whether these pin holes can meet the position tolerance requirements of the casting and do not affect machining. If there is an out-of-tolerance position after machining, it is very likely that the out-of-tolerance position of the preset hole causes the tool to follow the wrong preset hole. The guide deviates from the preset machining size.The base of reserved hole is the manufacturing base of the mold, and in the process of machining the selection of the process base and mold manufacturing base is not consistent, reserved hole must also deviate from the process base, so it will lead to the position out of tolerance.
This kind of problem can be solved in the following ways:
(1)When designing the mold, the mold manufacturing benchmark is taken as the rough positioning benchmark for machining as far as possible. After the benchmark is unified, the position accuracy of hole machining will be improved. For example, the reserved hole with position requirement should be the same as the positioning surface of the process reference on the parting surface of the mold side, reduce the error influence of mold clamping dislocation.
(2)Due to the diversity of products, it is sometimes difficult to unify the manufacturing standards. At this time, it is suggested to cancel the reserved hole with shallow processing depth.
(3)The positioning and processing of the hole are completed by machining, thus eliminating the guiding effect of the preset bottom hole and improving the position accuracy. However, it should also be noted that a large margin of cutting will expose defects in the die casting.
2.Influence of Reserved Hole on Machining Positioning
In machining, the reserved hole of the blank on the die casting is often used as coarse positioning, so the reliability of the reserved bottom hole is especially important for positioning. It is important, so it is suggested to consider the priority of preset hole positioning.
(1)The core of the reserved hole of the mold should be integrated with the core as much as possible, avoiding the use of detachable separate body. The main reason is that the split detachable core is used-after a period of time, burrs will be formed on the pin hole assembly joint surface, and these burrs are very thin and soft. Even if they are removed, a small part of them will adhere to the hole wall, affecting the positioning accuracy.
(2)Preset hole core for positioning
The inclination of the mould is enlarged and the surface hardness is increased as much as possible, so that the mould can be released smoothly during die casting production, the possibility of sticking the mould and pulling the inner wall of the hole can be reduced, and the positioning accuracy can be improved.
(3)When the reserved hole with small aperture and split type is used as coarse positioning reference, it is better to prepare more cores of the hole while making the mold, so as to ensure the stability and consistency of the hole size during mold maintenance and avoid unnecessary losses for subsequent machining. Whether the reserved hole is appropriate or not will affect the positioning and accuracy of machining. Therefore, in the die-casting production process, in addition to paying attention to whether the reserved hole is deformed or not, stick mold and other quality states, it is also necessary to strengthen the daily core maintenance, to ensure the consistency of positioning benchmark.
3rd Conclusion
To sum up, from the perspective of casting machining, the mold design is more convenient to locate and the surplus distribution is more reasonable, especially the manufacturing standard of the mold should be in good agreement with the machining process, which is beneficial to improving the efficiency and quality of machining. Therefore, in the design of die casting molds, designers need to consider all aspects of factors comprehensively, which puts forward new requirements for the expansion of professional ability of die designers. An excellent die casting designer must be a compound technical talent with mold technology, die casting technology and machining technology.
Comentários