Stable, Like a CAMEL
Important Notice:
Our company name is "Shenzhen Camel Die".
Please note that "Camel Die" is a separate entity and is not affiliated with us in any way. Our email address is @cameldie.com
We urge our customers and partners to verify the correct contact information to avoid any confusion or miscommunication.
Mold Making & Die Casting Mold Manufacturing Process
Mold Making
Mold Making refers to the processing of forming and blanking tools, in addition to shearing and die-cutting dies. Normally, the mold consists of two parts: the cavity die and the core die. A steel plate is placed between the upper and lower dies, and the material is molded under the action of a press. When the press is opened, the workpiece defined by the shape of the die is obtained, or the corresponding scrap is removed. Workpieces were as small as an electronic connector or as large as an automotive dashboard can be formed with a die. A progressive die is a set of dies that automatically moves the machined workpiece from one station to another and gets the molded part at the last station. Die processing process includes: cutting die, blanking die, compound die, extrusion die, four-slide die, progressive die, stamping die, die cutting die, etc.
Die Casting Mold Manufacturing Process
Die-casting materials, die-casting machines, and molds are the three significant elements of die-casting production, and none of them are indispensable. The so-called die-casting process is the organic and comprehensive application of these three elements to enable stable, rhythmic, and efficient production of qualified castings with good appearance, internal quality, and dimensions that meet the requirements of the drawing or agreement, or even high-quality castings.
The Latest Technology
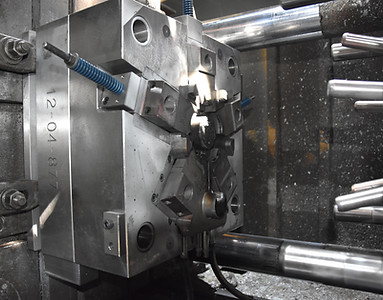
Die Casting Mold
Die casting mold is a tool for die casting metal parts, a tool for completing the die casting process on a dedicated die casting die forging machine. The basic process of CAMEL die-casting is first low-speed or high-speed casting of molten metal into the mold's cavity. Next, the mold has a movable cavity surface, which is pressurized forged with the cooling process of the molten metal, which eliminates the shrinkage of the blank. Shrinkage defects also make the internal structure of the blank reach broken grains in the forged state. As a result, the comprehensive mechanical properties of the blank have been significantly improved.
A variety of new die-casting mold surface treatment technologies continue to emerge, but generally can be divided into the following three categories:
(1) Improved technology of traditional heat treatment process;
(2) Surface modification technology, including surface thermal expansion treatment, surface phase change strengthening, electric spark strengthening technology, etc.;
(3) Coating technology, including electroless plating, etc.
Die-casting molds are a large category of molds. It is still difficult to meet the ever-increasing performance requirements by relying only on the application of new mold materials. Various surface treatment technologies must be applied to the surface treatment of die-casting molds in order to achieve Requirements for high efficiency, high precision, and long life. Among various molds, the working conditions of die-casting molds are relatively harsh. Die casting is to fill the mold cavity with molten metal under high pressure and high speed and die-casting. It repeatedly contacts the hot metal during the working process. Therefore, the die-casting mold is required to have high thermal fatigue, thermal conductivity, wear resistance, and corrosion resistance. , Impact toughness, red hardness, good mold release, etc. Therefore, the surface treatment technology requirements for die-casting molds are relatively high.
2. Surface modification technology
-
Surface thermal diffusion technology
This type includes carburizing, nitriding, boronizing, carbonitriding, sulfur carbonitriding, and so on.
-
Carburizing and carbonitriding
The carburizing process is used in cold, hot work and surface strengthening of plastic molds, which can improve the life of the mold. For example, the die-casting mold made of 3Cr2W8V steel is first carburized, quenched at 1140~1150℃, and tempered twice at 550℃. As a result, the surface hardness can reach HRC56~61, which increases the die life of die-casting non-ferrous metals and their alloys by 1.8~3.0 times. When carburizing, the main process methods include solid powder carburizing, gas carburizing, vacuum carburizing, ion carburizing, and carbonitriding formed by adding nitrogen to the carburizing atmosphere. Among them, vacuum carburizing and ion carburizing are technologies that have been developed in the past 20 years. This technology has the characteristics of fast carburizing, uniform carburizing, smooth carbon concentration gradient, and small deformation of the workpiece. It will be used on the surface of the mold, especially the precision mold. Play an increasingly important role in surface treatment.
1. Improved technology of traditional heat treatment process
The traditional heat treatment process of die-casting molds is quenching-tempering, and later surface treatment technology has been developed. Due to the variety of materials that can be used as die-casting molds, the same surface treatment technology and process applied to different materials will produce different effects. CAMEL proposes substrate pretreatment technology for mold substrate and surface treatment technology. On the basis of traditional technology, it proposes suitable processing technology for different mold materials to improve mold performance and increase mold life. Another development direction for the improvement of heat treatment technology is to combine traditional heat treatment technology with advanced surface treatment technology to increase the service life of die-casting molds. For example, the chemical heat treatment method carbonitriding, NQN combined with the conventional quenching and tempering process (namely carbonitriding-quenching-carbonitriding composite strengthening, not only obtains higher surface hardness, but also effective hardening layer The depth increases, the hardness gradient distribution of the infiltrated layer is reasonable, the tempering stability and the corrosion resistance are improved, so that while the die-casting mold obtains good core performance, the surface quality and performance are greatly improved.
3. Nitriding and related low-temperature thermal expansion technology
Including nitriding, ion nitriding, carbonitriding, oxygen nitriding, sulfur nitriding, and ternary sulfur carbon nitriding, oxygen, nitrogen, and sulfur. These methods have simple processing technology, strong adaptability, low diffusion temperature, generally 480-600°C, and small workpiece deformation. They are especially suitable for surface strengthening of precision molds. The nitride layer has high hardness, good wear resistance, and good impact resistance. The nitriding process is a commonly used process for surface treatment of die-casting molds, but when a thin and brittle white layer appears in the nitriding layer, it cannot resist the effect of alternating thermal stress and is prone to micro-cracks. Crack and reduce thermal fatigue resistance. Therefore, in the nitriding process, the process must be strictly controlled to avoid the formation of brittle layers.
Die casting and mold are both different and connected. The birth of the die-casting mold industry is a perfect combination of the two. In other words, die-casting, molds, and die-casting molds are three different industries, and their relationship mainly exists in several aspects. : Die-casting and mold integration, all molds are manufactured by ourselves, and rarely do molds for other companies; professional die-casting mold manufacturing, no die-casting; only die-casting, no mold manufacturing capabilities.