How Does CAMEL Do in Mold Temperature Control System Design and Heat Energy Balance Program
- mkt8280
- Aug 6, 2021
- 2 min read
What is mold temperature control? and how to balance the heat energy in the mold processing program? Then we introduce the related MTC, heat energy balance, and cooling system to propose solutions.
The Influence Of Mold Temperature On Mold And Die Casting
Mold temperature is one of the important factors affecting the quality of die castings, but it is often not strictly controlled during the production process. Especially in the production of complex die castings, only the temperature is controlled within a certain range to produce qualified die castings, and this temperature range is relatively narrow. At this time, the mold temperature must be strictly controlled.
In each die-casting cycle, the temperature in the mold cavity changes. The heat source to raise the temperature of the mold is the heat brought in by the molten metal, and the heat energy is converted into the part of the mechanical energy consumed by the molten metal to fill the cavity. When the mold receives heat, it also radiates heat to the surroundings. If the heat absorbed by the mold and the heat dissipated in a unit of time is equal and reaches an equilibrium state, it is called the heat energy balance of the mold.
What is MTC(Mold Temperature Controller)
The mold temperature controller controls the temperature of the mold during thermal equilibrium within the optimal working temperature of the mold. The temperature control of the mold is achieved through the heating and cooling system of the mold.
In the continuous die-casting process, the mold temperature goes through a cycle of rising and falling for each injection. In order to avoid the thermal shock of the molten metal on the low-temperature die-casting mold and shorten the life of the die, the molten metal will be chilled to lose fluidity, increase the line shrinkage, cause cracks or cracks to affect the quality of the die-casting, the mold must be fully preheated before die-casting.
In continuous production, especially when die-casting high melting point alloys, the mold heats up very quickly, causing the molten metal to stick to the mold, the die-casting part is pushed out and deformed, the mold is partially stuck or even damaged, and the mold opening time is prolonged, reducing the productivity, and the die-casting part cools slowly. And make the crystal grain coarse. Therefore, when the temperature of the die-casting mold is too high, cooling measures should be taken to keep the mold in thermal equilibrium.
How Does CAMEL Balancing Heat Energy
CAMEL designs ample cooling lines on the fixed side and movable side to control the heat energy balance to get the best cycle-time and part quality. The balanced heat energy also lowers the risk of die cracking.
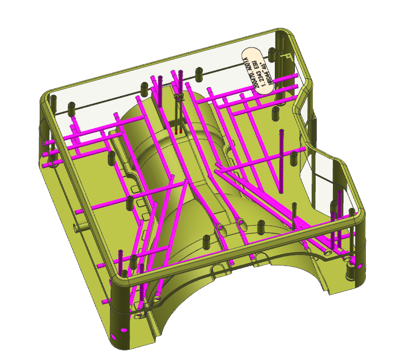

Comments