What is Mold Maintenance?
- Wilson_CAMEL
- Jul 2, 2021
- 3 min read
Updated: Jul 27, 2021
The die casting mold‘s working environment is very harsh, especially since the mold cavity part is easily damaged. This leads to the die casting metal liquid drilling into these gaps, producing serious flying edges or even jammed sliding parts. These problems of die casting mold will cause casting defects, and even cause a lot of scraps. In order to ensure the quality of the die-castings and extend the service life of the mold, CAMEL recommends the die casting workshop to carry out mold maintenance work such as inspection and repair of the molds.
Mold maintenance includes the following.
Observation And Inspection Of The Mold

There are 3 ways to check the mold,
On-site inspection of the mold, that is, the mold repairer inspects the mold before it is used;
The down-field inspection of the mold, that is, after producing a batch of castings, before the mold is put into storage, the mold repairer will check the condition of the mold;
Weekly inspection of the mold, inspection, and maintenance cycle can generally be determined by the number of press shots, generally every 10,000 press shots, the need to remove the mold from the die-casting machine, disassemble the main parts for an inspection and maintenance work, the content of the following.
(1) Observe the surface of the cavity to see if there are traces of strains and ablation of adhering metal chips, and polish the strains with abrasive cloth and polishing tools.
(2) Observe all the top bar, core whether there is bending, cracking and fracture, if necessary, a copper or wooden hammer gently knocking check, bending, cracking and fracture of the
Cores, projections, and top rods should be repaired or replaced immediately.
(3) Check whether all the top bar is free to move in and out, whether there is a jamming phenomenon, the top bar hole and other mating surface drilled into the metal fluid, the top bar end surface is high, or lower than the mold surface.
Problems found should be disassembled mold ejector parts for repair, the gap is too large for the top bar or sliding part to try to repair.
(4) Use a magnifying glass to observe whether the surface of the cavity is cracked, cracks, scratches, and local collapse, and there are pits and barbs on the surface of the mold wall in the direction of the release. For minor mesh cracks on the surface of the cavity, they can be reinforced with a tungsten reinforcing machine and then polished. For larger cracks, collapses, and pits, the bottom metal must be removed and the mold steel welding rod must be used for welding (preferably with argon arc welding to ensure the welding quality).
(5) Check if the exhaust system on the parting surface is clogged with grease or metal chips, and clean it up to ensure that the exhaust system is smooth.
(6) Check whether the cooling system of the mold is smooth and free from blockage.
Dimensional Accuracy Of Regular Identification
Die casting mold use after a certain period of time will appear the naked eye can not detect the deformation and wear, thus affecting the dimensional accuracy of die-castings and make the processing volume change.
Therefore, for the die-casting die with a high dimensional accuracy requirement, it is necessary to carry out the periodic identification of dimensional accuracy.
The identification period is decided according to the specific requirements, the identification method can be used to periodically check the die casting or use three coordinate measuring instruments for measurement.
Nitriding Treatment
Die casting die after a certain period of time, the surface nitriding layer will be worn, thus reducing the surface hardness of the cavity, increasing the tendency of die casting sticky mold.
For this reason, after every 30,000 die shots, the cavity should be disassembled, the surface should be polished and sent to the heat treatment workshop for nitriding treatment.
Tempering Treatment
Die casting die is used a certain number of times after the stress relief tempering treatment, According to improve the die casting die life of effective measures.
Tempering temperature should be 30~50% lower than the original tempering temperature of die-casting material.
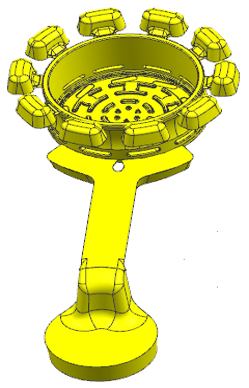
During mass production, the aluminum residue is commonly found at the bottom of the mold, which needs to be cleaned up regularly to avoid mold collision.
The stress-relieving tempering interval of aluminum alloy die casting mold is related to the die castings quality and the times of die casting shots, and usually:
die casting mass less than 0.1kg, shots of 25000 times;
die casting mass of 0.1kg-1kg, shots of 10000 times;
When the casting mass is more than 1kg, shots of 5000 times.
CAMEL deeply believes that good mold maintenance ensures a longer mold life and smooth production. Therefore, a quality mold must not only be stable during production but also easy to maintain.
LINK TO:
Comments